המונח shift left מקורו בעולם התוכנה והוא מתאר מצב בו צוותי הפיתוח מבצעים בדיקות איכות בשלבים מוקדמים במחזור חיי המוצר, להבדיל מכפי שהיה נהוג קודם לכן כאשר הבדיקות הללו התבצעו בתום תהליך הפיתוח. ככל שבעיות האיכות התגלו בשלבים מאוחרים יותר של התהליך, כך עלות ומשך זמן הטיפול בהן גדל, כמו גם ההשפעה על מועד השקת המוצר. תפיסת ה-shift left מעודדת זיהוי של בעיות שכאלו מוקדם ככל הניתן, עוד בתהליך הפיתוח, לטובת הפחתת הצורך בחזרה לאחור לטובת תיקונים, ובהתאם מצמצמת את עלויות הפיתוח ומקצרת את זמן יציאת המוצר לשוק. מתודולוגיית העבודה הזו אומצה בהמשך גם בעולמות הסייבר וניהול המוצר.
יישום התפיסה הזו בחברות חומרה יכול להשיג אפקט דומה, ולשפר את התהליך בהשוואה לאופן בו הוא מתנהל היום.
בתצורה הנוכחית של התהליך, מהנדס חומרה הבוחר רכיבים לטובת פיתוח מעגל חדש שוקל את התכונות הטכניות של הרכיבים, מחפש בספריית הרכיבים של הארגון, ולעיתים דוגם את המחירים ואת חיי המוצר של הרכיבים.
בסוף תהליך הפיתוח, הBoM (עץ המוצר) נשלח להנדסת הרכיבים ולצוות שרשרת האספקה להערכה. צוות ההנדסה מאתר תורפות ב- BoM כמו end of life (רכיב שאינו מיוצר יותר) ומציע רכיבים אלטרנטיביים המאופיינים בזמינות עדיפה. במקביל, מחלקת שרשרת האספקה בודקת את המחירים והזמינות של הרכיבים אצל היצרנים והספקים, ומוודאת שניתן למצוא אותם במחיר וזמן סבירים בהתאם לתוכנית העבודה והתקציב. רכיבים קשים להשגה או יקרים במיוחד נשלחים בחזרה למחלקת הפיתוח לעריכה מחדש והחלפתם.
התהליך עלול לחזור על עצמו מספר פעמים עד שמקובעת תצורת המוצר. במידה והתהליך הזה לא נעשה ביסודיות, יוצא ליצור מוצר שנשען על שרשרת אספקה שברירית, שעלויות ומשך זמן היצור שלו עלולים להשתנות דרמטית ממנה למנה, ובמקרי קיצון אף לא ניתן לייצרו כלל כתוצאה ממחסור ברכיבים. בנוסף, לאחר השקת המוצר ובמשך התקופה בה הוא מיוצר, התפתחויות בשוק מצריכות יישום של שינויים הנדסיים במוצר והחלפה של רכיבים (ECOs) המתניעים תהליך דומה למדי.
שימוש במתודולוגיית shift left ישנה את התהליך הזה מהיסוד.
צוות תכנון המוצר יוכל להטמיע שיקולי שרשרת אספקה בבחירת הרכיבים במידה ותהיה לו נגישות למידע בזמן אמת ומערכת המלצות והתרעות הממוקדים בשרשרת האספקה. אינדיקציות הנוגעות למחזור החיים, הזמינות ומחירי הפריטים, לדוג’, לצד המלצות על רכיבים חליפיים, יכולים לשפר דרמטית את תוצאות צוות התכנון בעת בחירת הרכיבים.
כתוצאה מכך, צוות התכנון יוכל להעמיד מוצר מהר הרבה יותר ותוך תלות קטנה בהרבה במחלקות האחרות, והמוצר יתאפיין בעלות אפקטיבית ובשרשרת אספקה אשר תהיה עמידה בפני הפרעות חיצוניות.
כיום, מחלקת שרשרת האספקה, ובאופן ספציפי אנשי הרכש, הם הראשונים לפגוש בעיות בשרשרת האספקה של הרכיבים. במקרים מסויימים ההתרעות מגיעות מיצרני הרכיבים ובמקרים אחרים הם נתקלים בקושי קונקרטי לרכוש רכיבים מסוימים.
לעיתים הפתרון היחיד לאותם חוסרים יהיה ביצוע שנוי הנדסי והחלפת אותם רכיבים ברכיבים זמינים יותר.
גם במקרה הזה, שימוש במתודולוגיית shift left ובמידע והכלים שהוזכרו קודם לכן, יקצר את התהליך וישפר את התוצאות.
זיהוי התורפות הללו בשלב מוקדם והצגת המלצות כיצד להתמודד איתן יפחית מאד את הסיכון לעצירה בשרשרת האספקה.
נגישות למידע בזמן אמת ושימוש בטכנולוגיות AI (בינה מלאכותית) לשיפור קבלת ההחלטות בארגון ואוטומציה של פעולות חזרתיות תאפשר לבנות ולתחזק שרשרת אספקה יעילה תוך צמצום המשאבים המושקעים בכך.
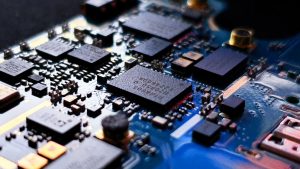
קרדיט תמונה: IKIDO
זהו גם העיקרון המנחה בפתרון ה- SaaS של חברת IKIDO (קרא עוד ב www.ikido.tech) שעושה שימוש במידע שנאסף בזמן אמת מעשרות מקורות ובמנוע AI כדי לסייע למהנדס המתכנן בבחירת רכיבים בעת תכנון כרטיס אלקטרוני, למהנדס הרכיבים בניהול תהליכי ECO ולמחלקת הרכש באיתור מקורות רכש אופטימליים לכל רכיב ורכיב.
גיא עירון, מייסד משותף ומנכ”ל IKIDO
בעל וותק של 15 שנה בניהול תפעול ושרשראות אספקה של יצור מערכות אלקטרומכניות מורכבות ו-IoT בחברות וותיקות ובחברות סטרטאפ.
קרדיט תמונות: IKIDO