במילון העברי לשתי המילים “טעות” ו”שגיאה” משמעות דומה. אבל יש הבדל דק ביניהן. טעות (mistake) – בחירה בדרך שאינה נכונה, כאשר בזמן הבחירה לא ידועה הדרך הנכונה. לעומתה שגיאה (error) היא בחירה בפתרון לא נכון או בדרך שאינה נכונה, כאשר בזמן הבחירה כל הנתונים הדרושים להחלטה נכונה, אמורים להיות ידועים. למשל: שגיאת כתיב, שגיאה גסה.
במאמר זה העליתי על הכתב מספר טעויות נפוצות בתכנון כרטיסים אלקטרוניים. פועל יוצא של טעויות אלו, אשר מתגלות לרוב במהלך ייצור והרכבת הכרטיס, עלול להיות קריטי בהשלכתו על איכות ואמינות הכרטיס, עלות הרכבתו ומשך זמן ההרכבה.
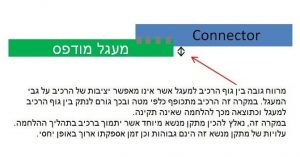
איור 1. בחירת רכיב הדורש ציוד מיוחד להרכבה
1. בחירת רכיבים לא מתאימה לטכנולוגיית הייצור
נטבח חשוב בתהליך תכנון כרטיס אלקטרוני הינו בחירת הרכיבים. בתהליך בחירת הרכיבים המאפיינים שנבדקים הן כמובן הפונקציונאליות של הרכיב והתאמתו לדרישות התכנון, עלות הרכיב וכן זמינותו בשוק. יחד עם זאת, ישנו מאפיין נוסף שראוי לבדקו והוא התאמת הרכיב לטכנולוגיית הייצור. בחירת רכיב שאינה מתאימה לטכנולוגיית הייצור, מאלצת הלחמה של הרכיב באמצעים אחרים שאינם סטנדרטיים. דבר זה, פוגם באיכות ההלחמה של הרכיב, מייקר את עלות העבודה, ומאריך את זמן הייצור.
להלן מספר דוגמאות לנושא:
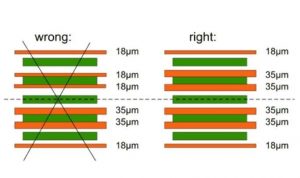
איור 2. תכנון סדר שכבות (Stack-Up) בכרטיס האלקטרוני
1.1 רכיב שאינו עומד בטמפרטורת ההלחמה –
כאשר מדובר על רכיב המיועד להלחמה בקו ייצור SMT יש לוודא כי האחרון עומד בטמפרטורת ההלחמה הטיפוסית בטכנולוגיה זו. בתהליך ייצור בטכנולוגיית SMT החום בתנור ההלחמה (REFLOW) מגיע לכ-230 מעלות צלזיוס בממוצע. קיימים רכיבים בשוק האלקטרוניקה, המוגדרים כרכיבי SMT אך טמפרטורת ההלחמה המקסימלית שלהם, כפי שמופיעה בדפי הנתונים של היצרן, הינה 100 מעלות צלסיוס. לאמור, רכיבים מסוג זה לא ניתן להרכיב בקו ייצור ה-SMT האוטומטי ולכן יש להרכיבם ידנית. במקרים בהם מדובר על מנת ייצור גדולה הדבר יכול לייקר משמעותית את עלות ההרכבה בכך שהלחמת הרכיב במקום להיות מבוצעת בקו הייצור בצורה אוטומטית מאלצת הרכבה ידנית שעלותה ואף זמן הרכבתה גבוהים משמעותית.
1.2 רכיב שאינו מיועד להלחמה בקו ייצור ה-SMT
קיימים מספר רכיבים אשר מוגדרים כרכיבי SMT אך מיועדים להלחמה באמצעות הלחמת מוליכים עדינים במכונות ייעודיות בטכנולוגיית Wire Bonding. רכיבים אלו לא ניתן להרכיב בקו ייצור ה-SMT הקונבנציונלי. אגב כך, יש לציין כי רכיב מסוג זה, עלות הרכבתו גבוהה באופן ניכר מעלות הרכבת רכיב SMT טיפוסי.
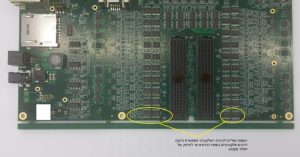
איור 3. הוספת שוליים לכרטיס האלקטרוני
1.3 בחירת מארזי רכיבים בקצה הטכנולוגיה ללא צורך –
הרכיבים האלקטרונים ניתנים לרוב להזמנה בכמה אפשרויות מבחינת גודלי המארזים. ככל שמארז הרכיב קטן יותר, כך הלחמתו בקו הייצור מורכבת יותר ועלולה לגרום לאיכות הלחמה שאינה מיטבית. לעיתים, מהנדסים בוחרים שלא במודע, מבין מספר חלופות של גדלי מארז הרכיב שמציע היצרן, דווקא בחלופה של המארז הקטן יותר. לדוגמא, בחירה ברכיב QFN בעל מארז Pitch (מרחק בין רגלי רכיב) של 0.35mm במקום מארז גדול יותר של אותו רכיב בעל Pitch של 0.65mm או אף מארז 0.5mm. במקרה ואין הכרח, בחירה במארז גדול יותר, תהיה בוודאות עדיפה יותר ותיטיב עם תוצאות הלחמת הרכיב בקו הייצור.
סעיף זה בא למעט כמובן מקרים בהם צפיפות הרכיבים על המעגל גבוהה במיוחד וכתוצאה מכך, לא ניתן להימנע משימוש במארזים קטנים של הרכיבים כדי לחסוך שטח יקר על גבי הכרטיס.
1.4 בחירת רכיב הדורש ציוד מיוחד להרכבה-
ישנם רכיבים אלקטרונים אשר הרכבתם על פני הכרטיס מחייבת שימוש בציוד ייעודי. דבר זה מייקר את הרכבת המעגל ויכול לגרום גם לתוצאת הלחמה שאינה איכותית דיה. לדוגמא, רכיב מסוג קונקטור SMT אשר בולט מקצה הכרטיס האלקטרוני בצורה ניכרת. (איור 1) עקב כך, שזנב הרכיב ארוך באופן יחסי, מרכז הכובד שלו נמצא מחוץ לכרטיס האלקטרוני ולכן הוא נוטה להתכופף כלפי מטה לאחר השמתו בקו ההרכבה. כיפוף זה, בצד אחד של הרכיב, גורן להתרוממות בצדו השני של הרכיב ובכך יוצר נתק, כלומר לחוסר הלחמה בין הפדים לבין גוף הרכיב. הוספת שוליים לקצה הכרטיס לא תעזור במקרה זה, כי גוף הרכיב גבוה מציר האפס האנכי של המעגל. כדי לבצע הלחמה מיטבית של רכיב זה, יש להזמין ציוד ייעודי מיוחד, אשר יאפשר תמיכה של גוף הרכיב וימנע את הכיפוף כלפי מטה. הזמנת ציוד זה טומנת בחובה כמובן עלויות נוספות ותשפיע גם על לוחות הזמנים של ההרכבה.
2. חוסר איזון תרמי בכרטיס האלקטרוני
תהליך הרכבת הכרטיס האלקטרוני בקו הייצור בטכנולוגיית ה SMT כוללת חימום של הכרטיס בתנור ההלחמה (REFLOW). הטמפרטורה המורגשת בתנור זה הינה גבוהה, באזור 230 מעלות צלסיוס. חום זה מתפשט על פני שטח הכרטיס האלקטרוני. במידה וקיים חוסר איזון תרמי כך שנוצרים בתהליך ההלחמה בין שתי נקודות על פני שטח הכרטיס הפרשי טמפרטורה (Delta T) ניכרים (למעלה מ-7 מעלות צלסיוס), הכרטיס יקבל שוק תרמי בשלב החימום בתנור ההלחמה. תוצאה של שוק תרמי זה יכולה להיות עקמומיות של הכרטיס, חוסר הלחמה ברכיבים מסוימים ועוד.
תופעה זו מושפעת רבות ממיקום הרכיבים האלקטרונים על גבי הכרטיס. הרכיבים האלקטרונים שנמצאים על גבי הכרטיס הינם הטרוגניים ויכולים לכלול רכיבים פאסיביים קטנים (כגון: נגדים, קבלים וכו’) שחתימת החום שלהם נמוכה, יחד עם רכיבים אקטיביים גדולים (כגון: רכיבי BGA, LGA) שחתימת החום שלהם גבוהה. ריכוז רכיבים אלקטרונים שחתימת החום שלהם גבוהה באזור מסוים בכרטיס ומנגד ריכוז רכיבים אלקטרונים שחתימת החום נמוכה באזור אחר בכרטיס, עלולה לגרום להפרשי טמפרטורה משמעותיים בין שני האזורים הנ”ל ובכך לגרום לשוק תרמי.
לכן, במהלך תכנון הכרטיס, חשוב מאוד לוודא כי נשמר האיזון התרמי על גבי הכרטיס.
אחת השיטות המומלצות למנוע שוק תרמי זה הינה לאפשר פיזור אחיד בשטח הכרטיס של הרכיבים שטמפרטורת ההלחמה שלהם גבוהה ולא לרכזן באזור מסוים אחד.
המלצה נוספת כדי לשמור על האיזון התרמי, הינה לוודא כי סדר השכבות (Stack Up) של הכרטיס הינו סימטרי. כלומר שכבות הנחושת ושכבות האדמה מחולקות באופן שווה ממרכז המעגל לכיוון שני צדדי המעגל. (איור 2)
3. חוסר תאימות בין טכנולוגיית הייצור וההרכבה
מחזור חיי הייצור של הכרטיס האלקטרוני כולל שני שלבים מרכזיים: ייצור הכרטיס עצמו וכן הרכבת הרכיבים על גבי הכרטיס. חוסר תאימות בטכנולוגיה בין שני שלבים אלו עלול להוביל לפסילת מנת הייצור. לדוגמא: הגדרת חומר גלם ליצרן הכרטיס המותאם לטכנולוגיית בדיל-עופרת ובה בעת הרכבת הכרטיס בטכנולוגיה ללא-עופרת. כלומר, בהנחיות ליצרן הכרטיס מצוין כי חומר הגלם צריך להיות תואם להרכבה בטכנולוגיית בדיל-עופרת אשר מאופיינת בטמפרטורה נמוכה באופן יחסי לדוגמא חומר גלם בעל (Tg = GLASS TRANSITION TEMPERATURE, טמפרטורה בה חומר הגלם עובר ממצב מוצק קשיח למצב גמיש-אלסטי). בה בעת, הרכבת הכרטיס הינה בטכנולוגית ללא-עופרת אשר מאופיינת בטמפרטורות הלחמה גבוהות, כ-40 מעלות צלסיוס יותר מאשר תהליך הרכבה בטכנולוגית בדיל-עופרת. לכן קיים כאן חוסר תאימות. כאשר כרטיס זה שחומר הגלם שלו מתאים לטמפרטורת הרכבה נמוכות, יורכב בטכנולוגיה ללא-עופרת המאופיין בטמפרטורת גבוהות, הכרטיס יקבל עיוותים בתהליך ההרכבה בתנור החימום, יגרום לתוצאת איכות ירודה ואף להביא לפסילת מנת הייצור. במקרה זה ראוי היה להגדיר ליצרן המעגל חומר גלם עם Tg גבוה יותר, כמו Tg-170 כדי לוודא שהכרטיס עמיד לטמפרטורות הגבוהות הנדרשות בתהליך הרכבה בטכנולוגיה ללא-עופרת.
4. מיקום רכיבים בקצה הכרטיס ללא שוליים
הכרטיס האלקטרוני עובר מתחנה לתחנה בקו ההרכבה על גבי מסוע. מסוע זה שנמצא לאורך כל פס הייצור, מורכב משתי מסילות מקבילות אשר הן הבסיס עליו יושב הכרטיס האלקטרוני בשלבי ההרכבה השונים. מסילות אלו הן בעלות מגרעת קטנה אשר מאפשרת את יציבות הכרטיס האלקטרוני על גבי המסוע. ההיטל של שטח המגרעת על הכרטיס, הינו אזור בו ראש המכונה אינו מגיע אליו ולכן אזור זה הינו אסור למיקום רכיבים. מיקום רכיבים אלקטרונים בקצה הכרטיס (>5 מ”מ)
עלול להקשות ואף למנוע, מראש המכונה להניח רכיבים אלו במדויק על גבי הכרטיס. לאור זאת, יש לוודא כי מוגדר שטח “סטיראלי” נקי מרכיבים במרחק של 5mm מקצה הכרטיס האלקטרוני. במקרים חריגים ניתן אף לרדת ממרחק זה, אך רק בתיאום מראש עם מרכיב המעגל.
במקרה, והכרטיס צפוף ונדרש לנצל את מלוא שטח הכרטיס לטובת מיקום הרכיבים, ניתן להיעזר בשוליים אשר ישמשו כבסיס התמיכה של הכרטיס במהלך הרכבתו בקו הייצור. כך ניתן יהיה להתקרב עם מיקום הרכיבים עד ל-1-1.5mm מקצה הכרטיס. במקרה זה, בקצה הכרטיס יוספו שוליים, רחבים דיים אשר יהוו את נקודת האחיזה של הכרטיס על מסילות מכונת ההרכבה. שוליים אלו יוסרו לאחר ההרכבה כדי לחזור למידת הכרטיס הגנרית. (איור 3)
5. מיקום נקודות ייחוס בקצה הכרטיס
נקודות הייחוס (Fiducials) המצוינות על הכרטיס האלקטרוני משמשות כנקודות ציון בהן נעזר ראש המכונה לאיתור המיקום המדויק של הרכיבים. מיקום והגדרה נכונה של נקודות אלו במהלך עריכת הכרטיס, הינו קרדינאלי בהשלכתו על איכות הרכבת הרכיבים על גבי הכרטיס האלקטרוני. בהתאם לנקודות אלו, מבצעות המכונות את הפעולות המדויקת כגון: מריחת משחת בדיל, השמת רכיבים, בדיקת ויזואלית (AOI), בדיקת רנטגן (X-RAY) ועוד. עקב כך, ששדה הראייה של ראש המכונה בקצה המעגל הינו מוגבל, מיקום נקודות ייחוס אלו בשפת במעגל, עלול לגרום לכך שראש מכונת ההשמה לא יוכל לזהות את הנקודות. ללא איתור נקודות הייחוס על ידי ראש המכונה, לא ניתן יהיה לבצע השמה של הרכיבים על גבי הכרטיס. לכן יש להקפיד ולהגדיר בשלב עריכת הכרטיס, את נקודות הייחוס החשובות הללו במרחק הגדול מ-7mm מקצה הכרטיס האלקטרוני.
בנוסף, יש לאפשר שחרור Soldermask, אשר ימנע את הסתרת הנקודה ויאפשר למכונה זיהוי מהיר, ברור ומדויק של נקודת הייחוס.
באותו הקשר, ראוי לציין כי מומלץ למקם 3 נקודות ייחוס על שטח הכרטיס בצורה א-סימטרית כדי לאפשר למכונה האוטומטית לזהות בצורה חד-חד ערכית כי המעגל הוכנס למסוע המכונה בכיוון הנכון. מיקום 4 נקודות ייחוס על פני הכרטיס בצורה סימטרית עלול לגרום לכך כי גם הכנסה הפוכה של הכרטיס תיקלט במכונה כתקינה ותגרום להשמה לא נכונה של הרכיבים.
כמו-כן, לטובת שימוש במכונות מריחת בדיל (Printer) אוטומטיות יש למקם נקודות ייחוס גם על קבצי ה-SolderMask וה-SolderPaste.
זאת ועוד, כדי שנקודת הייחוס תהיה ברורה וקלה לזיהוי במהלך שימוש במכונת הרנטגן (X-RAY), יש לשמור על אזור נקי מרכיבים (גדול מ-1mm) בצמוד לנקודות הייחוס לאורך כל עובי המעגל, דהיינו גם מצדו השני של הכרטיס. הסיבה היא שקרן הרנטגן חודרת לכל עובי הכרטיס ולכן מצלמת גם את צידו השני. מיקום רכיבים בצמוד (<1mm) לנקודות הייחוס בצדו השני של הכרטיס לא יאפשר זיהוי של הנקודה על-ידי מכונת הרנטגן ולכן יקשה מאוד על
תהליך הבדיקה במכונה זו.
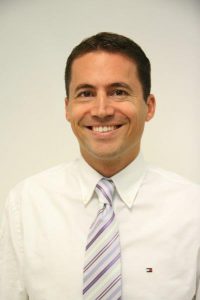
ארבל ניסן, סמנכ”ל שיווק, ניסטק
לסיכום, היה מי שאמר כי “טעות לעולם חוזרת, אבל כשהמחק נגמר לפני העיפרון – סימן שהגזמת.”
במאמר זה מניתי מספר טעויות נפוצות בתכנון ועריכה של כרטיסים אלקטרוניים. טעויות אלו נובעות לרוב מחוסר ידע של המהנדס ו/או של עורך המעגלים. לכן, מומלץ כי הגורמים המעורבים בתכנון הכרטיס האלקטרוני, יהיו בעלי ידע מספיק בטכנולוגיות הייצור וההרכבה. ראוי גם להתייעץ עם עורך המעגלים ועם מרכיב המעגלים ולהיעזר בניסיונם בתחום עוד בשלב תכנון הכרטיס כדי לוודא התאמתו לתהליכים אלו. סינרגיה בין שלב התכנון לשלב הייצור תוודא כי הטעות לעולם לא תחזור.